As we all know, buildings are generally expected to have a service life of at least 50 years. Therefore, the materials used must also have a long service life. Silicone sealant has been widely used in the field of building waterproofing and sealing due to its excellent high and low temperature resistance, outstanding weather aging resistance, and good bonding properties. However, after a period of time following construction, discoloration of silicone sealant has become a frequent issue, which leaves abrupt “lines” on buildings.
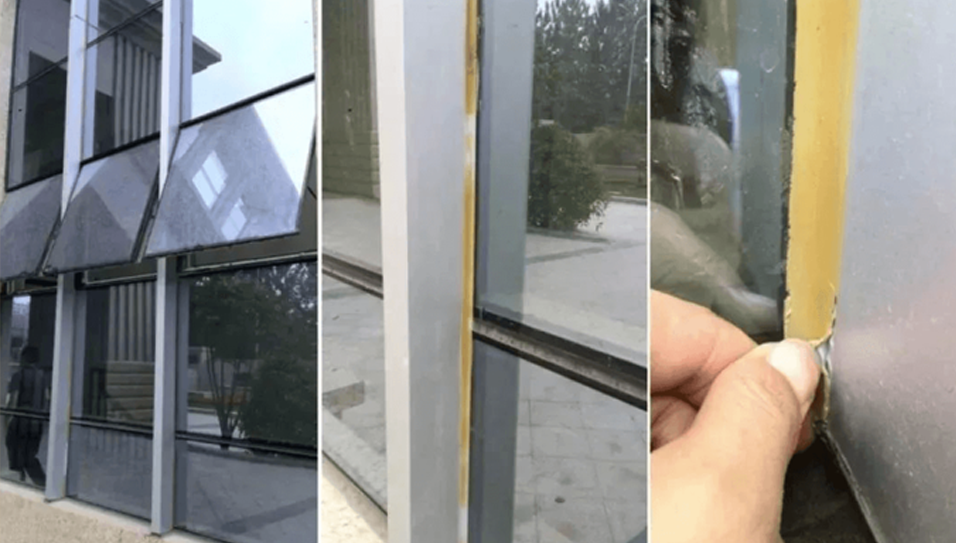
Why does silicone glue change color after use?
There are many reasons for partial or complete discoloration of silicone tunnel sealant or glass glue, mainly in the following aspects:
1. Incompatibility of different sealant materials Acidic sealants, neutral alcohol-based sealants, and neutral oxime-based sealants cannot be used together, as they can affect each other and cause discoloration. Acidic glass sealants can cause oxime-based sealants to turn yellow, and using neutral oxime-based and neutral alcohol-based glass sealants together can also cause yellowing.
The molecules released during the curing of neutral oxime-type sealants, -C=N-OH, can react with acids to form amino groups, which are easily oxidized by oxygen in the air to form colored substances, leading to discoloration of the sealant.
2. Contact with rubber and other materials
Silicone sealants may turn yellow when in direct contact with certain types of rubber, such as natural rubber, neoprene rubber, and EPDM rubber. These rubbers are widely used in curtain walls and windows/doors as rubber strips, gaskets, and other components. This discoloration is characterized by unevenness, with only the parts in direct contact with the rubber turning yellow while other areas remain unaffected
3. Sealant discoloration can also be caused by excessive stretching
This phenomenon is often mistakenly attributed to color loss of the sealant, which can be caused by three common factors.
1)The sealant used has exceeded its displacement ability and the joint has been stretched excessively.
2) The thickness of the sealant in certain areas is too thin, resulting in color changes concentrated in those areas.
4. The discoloration of sealant can also be caused by environmental factors.
This type of discoloration is more common in neutral oxime-type sealants, and the main reason for the discoloration is the presence of acidic substances in the air. There are many sources of acidic substances in the air, such as curing acidic silicone sealant, acrylic coatings used in construction, high levels of sulfur dioxide in the atmosphere during winter in northern regions, burning plastic waste, burning asphalt, and more. All of these acidic substances in the air can cause oxime-type sealants to discolor.
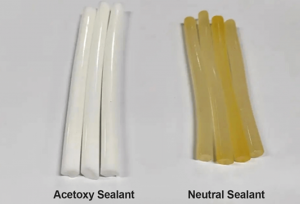
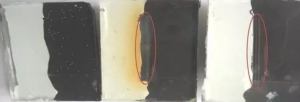
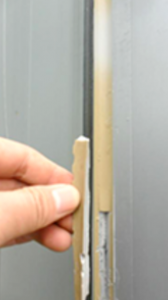
How to avoid discoloration of silicone sealant?
1) Before construction, conduct a compatibility test on the materials in contact with the sealant to ensure compatibility between the materials, or choose more compatible accessory materials, such as selecting silicone rubber products instead of rubber products to reduce the probability of yellowing.
2) During construction, neutral sealant should not be in contact with acid sealant. The amine substances produced by the decomposition of neutral sealant after encountering acid will oxidize in the air and cause discoloration.
3) Avoid contact or exposure of the sealant to corrosive environments such as acids and alkalis.
4) Discoloration mainly occurs in light-colored, white, and transparent products. Choosing dark or black sealants can reduce the risk of discoloration.
5) Choose sealants with guaranteed quality and good brand reputation-JUNBOND.
Post time: May-22-2023